China High Pure Isostatic Graphite Mold for Aerospace Industry
Graphite Mold Manufacturer, Graphite Mould Exporter & Supplier in China- Beijing Guang Xin Guo NengTechnology Co. Ltd.
Product Description
China High Pure Isostatic Graphite Mold for Aerospace Industry
Graphite mold is an allotrope of elemental carbon. The periphery of each carbon atom is connected with three other carbon atoms by covalent bonds to form covalent molecules. Since each carbon atom emits an electron, those electrons can move freely, so graphite belongs to a conductor.
The graphite mold has good chemical stability. Specially processed graphite has the characteristics of corrosion resistance, good thermal conductivity, and low permeability. It is widely used in the manufacture of heat exchangers, reaction tanks, condensers, combustion towers, absorption towers, coolers, heaters, filters , Pump equipment. It is widely used in petrochemical industry, hydrometallurgy, acid-base production, synthetic fiber, papermaking and other industrial sectors, which can save a lot of metal materials.
Graphite molds are used for casting, sand turning, compression molding and high-temperature metallurgical materials: due to the small thermal expansion coefficient of graphite and resistance to rapid cooling and rapid heat changes, it can be used as a casting mold for glassware. After using graphite, the ferrous metal can obtain accurate casting size and surface finish rate High, can be used without processing or a little processing, thus saving a lot of metal. Production of powder metallurgy processes such as cemented carbide, usually using graphite materials to make ceramic boats for stamping and sintering. Single crystal silicon crystal growth crucibles, area refining vessels, support fixtures, induction heaters, etc. are all made of high-purity graphite. In addition, graphite can also be used as a vacuum smelting graphite insulation board and base, high temperature resistance furnace tube, rod, plate, grid and other components.
Six excellent properties of graphite mold:
1. Excellent thermal and electrical conductivity
2. Very good thermal stability and resistance to heating shock due to low linear expansion coefficient
3. Resistant to chemical corrosion and multi-metals are not easy to react
4. At high temperature (in the sintering temperature of most copper-based carcass above 800℃), the strength increases with increasing temperature
5. Has good lubrication and wear resistance
6. It is easy to process and has good mechanical processing performance. It can be made into a mold with complex shape and high precision.
Nowadays, graphite mold design has been transformed from artificial experience design to relying on computer-aided design. Modern graphite mold enterprises all widely use computer-aided technology and artificial intelligence technology to make decisions. Simulation analysis and optimization design. At the same time, the application of database and computer network technology allows designers to share design information, information, resources and cooperation on a larger scale, so that the overall level of modern graphite mold design has risen to an unprecedented height.
Application of graphite mold
At present, graphite molds are widely used mainly in the following aspects:
1. Graphite molds for continuous casting and semi-continuous casting of non-ferrous metals: In recent years, domestic and foreign countries are promoting advanced production methods such as direct continuous (or semi-continuous) manufacturing of rods or pipes from the molten metal state. Domestically, this method has been adopted in copper, copper alloy, aluminum, aluminum alloy and so on. Artificial graphite is considered to be the most suitable material as a mold for continuous casting or semi-continuous casting of non-ferrous metals. Production practice proves that due to the use of graphite mold, due to its good thermal conductivity (the thermal conductivity determines the solidification speed of the metal or alloy), the mold's self-lubricating performance and other factors not only increase the mold speed, but also due to the size of the ingot Accurate, smooth surface, uniform crystal structure, can be directly processed in the next procedure. This not only greatly improves the yield rate and reduces the loss of waste products, but also greatly improves the quality of products. There are two types of continuous casting methods: vertical continuous casting and horizontal continuous casting.
2. Graphite moulds for pressure casting: Artificial graphite materials have been successfully used for pressure casting of non-ferrous metals. For example, zinc alloy and copper alloy castings produced by pressure casting molds made of artificial graphite materials have been used in automobile parts, etc.
3. Graphite mold for centrifugal casting: Graphite mold has been successfully used in centrifugal casting. The United States has used artificial graphite casting molds with a wall thickness of more than 25 mm to centrifugally cast bronze bushings. In order to prevent the artificial graphite mold from burning, certain anti-oxidation measures can be taken. After casting a certain number of castings, if it is found that the inner surface of the mold is burned, the size of the inner hole of the mold can be enlarged to be used for casting large-size casings.
4. graphite hot-pressing die mold: The artificial graphite hot-pressing die used in the pressure sintering of cemented carbide has the following characteristics: First, if the pressing temperature is increased to 1350-1450 degrees, the required unit pressure can be reduced to 67-100 kgf/cm2 (that is, 1/10 of the cold-pressing pressure) is sufficient; second, pressurization and heating are performed in the same process, and a compact sintered body can be obtained after a short time of sintering.
5. Graphite molds for glass forming: Because graphite materials are chemically stable and are not easily infiltrated by molten glass, they do not change the composition of the glass. Graphite materials have good thermal shock resistance and small changes in temperature with temperature. It has become an indispensable mold material in manufacturing, and it can be used to manufacture glass tubes, elbows, funnels and other various shaped glass bottle casting molds.
6. Graphite sintering dies and other diamond sintering dies: Utilizing the characteristics of minimal thermal deformation of artificial graphite materials, sintering dies and brackets for transistors can be manufactured, which are now widely used and it has become an indispensable material for the development of the semiconductor industry. In addition, graphite molds are also used in casting molds for cast iron, durable casting molds for various non-ferrous metals, casting molds for cast steel, casting molds for heat-resistant metals (titanium, zirconium, molybdenum, etc.) and aluminum for welding rails. Hot-welded molds, etc. Graphite molds for hot-pressed sintered diamond tools bear the dual roles of heating element and mold support in the diamond tool manufacturing process. The quality of graphite molds directly affects the dimensional accuracy and appearance of diamond tools. Hot pressing sintering process requirements: temperature reaches (1 000 ± 2) ℃, molding pressure 16 ~ 50 MPa, heat preservation pressure retention time is 15 ~ 30 min, the environment is non-vacuum state. Under this working condition, not only the graphite mold of the forming and heating element is required to have electrical conductivity, high resistivity, and sufficient mechanical strength, but also it needs to have good oxidation resistance and a long service life to ensure diamond The dimensional accuracy and excellent performance of the tool. At present, graphite mold materials for diamond tool manufacturing in western developed countries are mainly graphite materials with ultra-fine particle structure, high purity and high graphitization degree, and their average particle size is required to be less than 15μm, even below 10μm, and medium pore size is less than 2μm. The graphite mold made of this carbon raw material has small porosity, dense structure, high surface finish, strong oxidation resistance, and an average service life of 30 to 40 times. Diamond molds require high hardness, good oxidation resistance, and high processing accuracy. The use of high-quality graphite raw materials greatly extends the service life of the mold and improves its oxidation resistance.
7. Graphite EDM processing
Moulds are increasingly becoming the main process equipment for industrial mass production in the fields of household appliances, automobiles, electromechanics, aerospace and other industries, and undertake the processing and production of 60%-90% of product parts in these industries. In recent years, high-speed milling has broken through the limitation that traditional milling is difficult to process high-hardness, high-strength, high-toughness mold materials. However, EDM has the advantages of high processing accuracy and high surface quality, and a wide processing range, especially in the processing of mold cavities of complex, precise, thin-walled, narrow slits, and high-hard materials, which is unmatched by high-speed milling. EDM will still be the main means of mold cavity machining. Graphite electrodes (compared to copper) have the advantages of low electrode consumption, fast discharge machining speed, good machining performance, light weight, and small thermal expansion coefficient. They gradually replace copper electrodes and become the mainstream of electroprocessing electrodes. Compared with copper, graphite electrodes have the advantages of low consumption, fast discharge speed, light weight and small thermal expansion coefficient. Therefore, they gradually replace copper electrodes and become the mainstream of discharge machining electrodes.
Product Parameters
Category | Bulk Density | Resistivity | Shore Hardness | Flexural Strength | Compressive Strength | Young's Modulus | Porosity | Ash Content | Grain Size | Coefficient of Thermal Expansion | Thermal Conductivity | Application Fields | |
g/cm³ | μΩm | HSD | Mpa | Mpa | Gpa | % | PPM | μm | (indoor temp~600℃) 10^-6/℃ | (100℃) W/m﹒k | |||
Molded Graphite | GXMG-1 | 1.65 | 11~14 | 30 | 15 | 28 | 15 | 23% | / | 4mm | 2.6 | 50~60 | Crucible, Conventional Cast, etc |
GXMG-2 | 1.68 | 11~14 | 35 | 17 | 35 | 13 | 20% | / | 2mm | 3.5 | 60~80 | Crucible, Conventional Cast, Carbon Brushest, etc | |
GXMG-3 | 1.70 | 10~13 | 42 | 15 | 35 | 14 | 18% | / | 0.8mm | 1.8 | 62~80 | Crucible, Alloy Cast, Carbon Brushest, etc | |
GXMG-4 | 1.72 | 10~13 | 42 | 24 | 40 | 13 | 17% | / | 0.8mm | 1.5 | 65~85 | Crucible, Alloy Cast, Sintering Mold, Rodt, etc | |
GXMG-5 | 1.75 | 10~13 | 45 | 28 | 55 | 13 | 15% | 800 | / | 1.8 | 65~85 | Crucible, Alloy Cast, Sintering Mold, Continuous casting Mold, Rodt, etc | |
GXMG-6 | 1.78 | 9~12 | 46 | 28 | 58 | 12 | 12% | 800 | / | 4.5 | 80~100 | Crucible, Alloy Cast, Sintering Mold, Continuous casting Mold, Rod, Furnacet, etc | |
Isostatic Graphite | GXIG-1 | 1.75 | 10~13 | 42 | 35 | 60 | 9 | 16% | 500 | 13~18μm | 4.8 | 80~120 | Crucible, Alloy Cast, Sintering Mold, Continuous casting Mold, Rod, Furnacet, etc |
GXIG-2 | 1.78 | 9~12 | 42~50 | 38 | 70 | 10 | 12% | 500 | 10~15μm | 4.8 | 80~100 | Crucible, Alloy Cast, Sintering Mold, Continuous casting Mold, Rod, Furnacet, etc | |
GXIG-3 | 1.80 | 9~13 | 45~60 | 40 | 95 | 11 | 12% | 500 | 9~15μm | 4.8 | 85~110 | EDM, Furnace, Sintering Mold, Noble Metal Metallurgyt, etc | |
GXIG-4 | 1.82 | 9~13 | 50 | 46 | 96 | 10 | 12% | 500 | 13~15μm | 5 | 90~110 | photovoltaic, EDM, Sintering Mold, Noble Metal Metallurgyt, etc | |
GXIG-5 | 1.85 | 9~12 | 48 | 48 | 95 | 11 | 12% | 500 | 13~15μm | 5 | 95~115 | ||
GXIG-6 | 1.88 | 9~15 | 60 | 52 | 110 | 10 | 8% | 500 | 8~10μm | 5.5 | 95~120 | Fuel Cell, 3D Glass Moldt, etc | |
GXIG-7 | 1.90 | 9~14 | 70 | 55 | 125 | 11 | / | / | 8~10μm | 5.5 | 100~130 | Semiconductor, photovoltaict, etc | |
Mechanical graphite | M106H | 1.69~1.78 | / | 75 | 60 | 160 | / | 3% | / | / | 4.0 | 13 | Sealing, bearing, compressor carbon vane, pump accessories (temperature tolerance: <220℃)t, etc |
M120K | 1.7~1.85 | / | 75 | 62 | 150 | / | 3% | / | / | 4.0 | 13 | ||
M106D | 2.2~2.3 | / | 70 | 60 | 160 | / | 2% | / | / | 4.0 | 15 | Sealing, bearing (temperature tolerance:<350℃ under aerobic conditions, <550℃ under anaerobic conditions)t, etc | |
M120D | 2.2~2.3 | / | 75 | 65 | 160 | / | 2% | / | / | 4.0 | 15 | ||
M170D | 2.2~2.3 | / | 80 | 65 | 180 | / | 2% | / | / | 4.0 | 15 |
Packing & Delivery
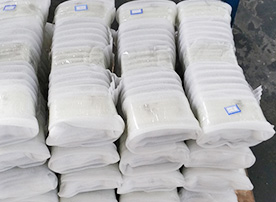
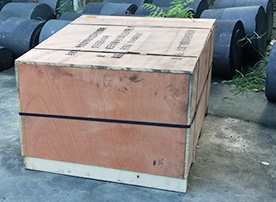
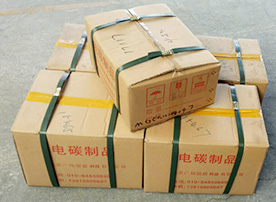
1. Inside: use PE packaging and paste specification parameters
2. For short-distance: use carton packaging & inside foam board filling up interspace (appearance can be selected without text)
3. For long-distance transportation using carton + plywood box packaging (appearance of DIY text)
4. Delivery Port: Tianjin
Graphite Products Lead Time: 10-15 days after the order confirmation. Delivery by Express, Air also accepted.
FAQ
Q1. Are you a factory or trading company?
Q2. Can you introduce your main products?
Beijing Guang Xin Guo Neng Technology Co., Ltd mainly produce graphite products, we can offer customized shape according to customers' specific demand. Our Graphite Products, include extruded graphite products, vibration moulding graphite products, molded graphite products, isostatic graphite products. We can produce a lot of graphite products, like graphite mold, graphite casting die, graphite heating element, graphite crucible, graphite sealing ring, graphite tube, graphite rod, graphite edm, graphite block etc.
Q3.What is your MOQ?
Q4. Can you offer free samples?
Q5. When can I get the price?
Q6. Do you accept OEM or ODM orders?
Q7. How about your delivery time?
Q8. Do you test your goods before delivery?
Q9. How do you keep long-term business relationship?
Notice: When you contact us, please show us the accurate drawing and your selected graphite material information, then we can offer you accurate price.